CNC Precision Machining Factory: Elevating Metal Fabrication Standards
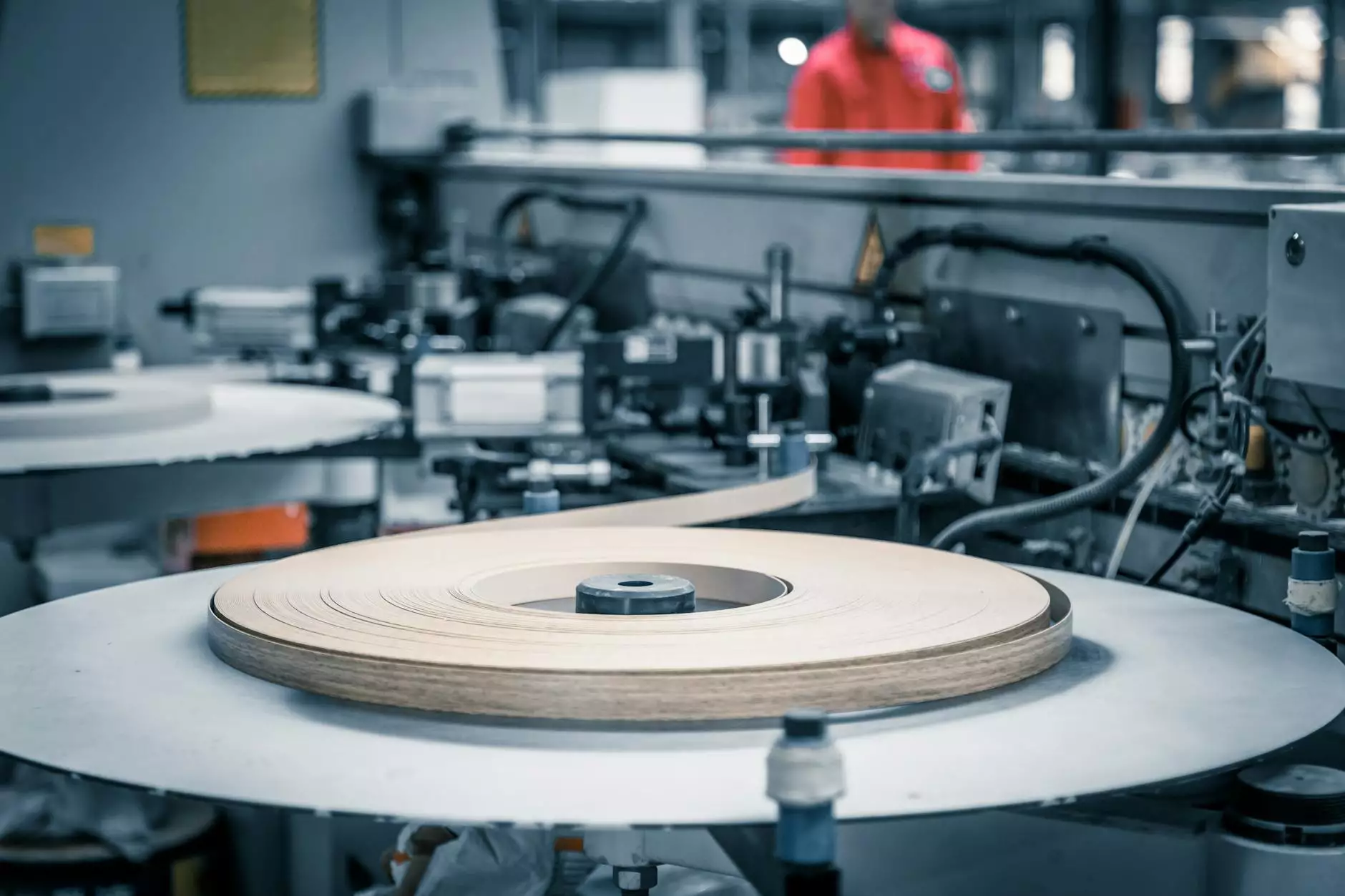
In today's fast-paced manufacturing landscape, the demand for high-quality, precise components is paramount. To meet these challenges, a CNC precision machining factory represents a formidable solution, intertwining cutting-edge technology with exceptional craftsmanship. This article delves into the world of CNC precision machining, exploring its importance in metal fabrication, the processes involved, and the numerous advantages it offers to businesses in various industries.
Understanding CNC Precision Machining
CNC (Computer Numerical Control) precision machining refers to the automated control of machining tools by means of a computer. It allows for the precise shaping of materials like metal, plastic, and composites, resulting in high tolerance and intricate designs that manual machining cannot achieve. But what makes it so valuable? Consider the following:
- Automation: CNC machines automate the machining process, reducing the need for manual intervention and thus minimizing human error.
- Precision: CNC machining can achieve tolerances of 0.001 inches or better, ensuring components fit perfectly into larger assemblies.
- Consistency: Once a design is programmed into the CNC machine, it can replicate the process with exactitude, ensuring that every piece is identical.
- Complexity: CNC machines can create complex geometries and detailed designs, making them perfect for custom projects.
The Role of CNC Precision Machining in Metal Fabrication
The metal fabrication industry is evolving, and a CNC precision machining factory is at the forefront of this transformation. Here’s how:
1. Enhanced Efficiency
Efficiency is crucial in metal fabrication. CNC machines can operate continuously, significantly increasing production rates compared to traditional methods. This not only boosts output but also reduces lead times, enabling manufacturers to meet tight deadlines.
2. Cost-Effectiveness
Although the initial investment in CNC machinery can be substantial, the long-term savings are significant. The reduction in waste, lower labor costs due to automation, and the ability to produce high-quality parts that require less post-processing make CNC machining a cost-effective solution for many businesses.
3. Customization Capabilities
Businesses often require customized parts for their products. With CNC precision machining, custom designs can be easily programmed and executed. This is especially advantageous for industries such as aerospace, automotive, and medical devices, where unique specifications are common.
The Process of CNC Precision Machining
The CNC precision machining process involves several key steps, each vital in producing high-quality products:
1. CAD Design
The journey begins with a CAD (Computer-Aided Design) model. Designers create detailed 3D models of the components, including specifications and tolerances.
2. CAM Programming
Once the design is complete, it is converted into a CAM (Computer-Aided Manufacturing) program. This program translates the design into machine code that the CNC machine can understand.
3. Tool Selection
Choosing the right tooling is crucial. The materials to be machined determine the type of tools needed, whether they be end mills, drills, or lathes.
4. Machining Process
During machining, the CNC machine precisely follows the programmed instructions to remove material from the workpiece, creating the desired shape. This can involve various operations, such as:
- Milling: Cutting material away from a workpiece using rotary cutters.
- Turning: Rotating the material against a stationary cutting tool.
- Drilling: Creating holes using a rotating drill bit.
- EDM (Electrical Discharge Machining): Using electrical discharges to remove material from electrically conductive metals.
5. Quality Control
After machining, rigorous quality control ensures that each component meets the specified tolerances and quality standards. This might involve using advanced measuring tools like coordinate measuring machines (CMM) or optical comparators.
Benefits of Using a CNC Precision Machining Factory
Utilizing services from a CNC precision machining factory offers a multitude of advantages for businesses looking to enhance their manufacturing processes:
1. Accessibility to Advanced Technology
Many CNC precision machining factories invest in the latest technology and equipment. This provides businesses access to advanced machining capabilities without the heavy investment associated with purchasing and maintaining such equipment themselves.
2. Scalability
CNC machining is highly scalable, accommodating large production runs or small batch orders with ease. This flexibility is crucial for businesses that experience seasonal demand fluctuations or require rapid prototyping solutions.
3. Expertise and Experience
Working with experienced machinists and engineers in a CNC precision machining factory can significantly enhance product quality. Their expertise in material science, machining processes, and design optimization can help troubleshoot issues and improve designs.
Industries Benefiting from CNC Precision Machining
CNC precision machining is not confined to any singular industry. In fact, its versatility allows it to serve a wide range of sectors:
- Aerospace: Components for airframes, engines, and other critical systems require high precision and quality.
- Automotive: From engine components to custom parts, CNC machining is integral to modern vehicle manufacturing.
- Medical: Medical devices and equipment require strict adherence to regulations and standards that CNC machining can fulfill.
- Electronics: Housing and components for electronic devices benefit from the precision and complexity achievable through CNC machining.
- Architectural: Custom fittings and fixtures can be produced accurately to meet specific design requirements.
Future Trends in CNC Precision Machining
The field of CNC precision machining is constantly evolving, and staying ahead of trends is essential for businesses looking to maintain a competitive edge. Some of the anticipated trends include:
1. Integration of AI and Machine Learning
The integration of artificial intelligence (AI) and machine learning into CNC machining operations is expected to optimize production processes, monitor equipment health, and enhance predictive maintenance.
2. Increased Customization
As consumer demands shift toward personalized products, the ability to quickly adjust CNC machining processes to accommodate bespoke orders will be critical.
3. Sustainable Manufacturing Practices
With increasing awareness of environmental responsibilities, CNC precision machining factories will need to implement greener practices, including waste reduction and energy-efficient technologies.
Conclusion
The emergence of CNC precision machining factories marks a pivotal development in the metal fabrication industry. By leveraging advanced technology and skilled craftsmanship, these facilities not only enhance manufacturing precision but also contribute to increased efficiency, cost savings, and innovation. As businesses continue to seek greater quality and adaptability in their production processes, the role of these factories will undoubtedly grow, propelling industries toward a more productive and custom-fit future.
For businesses looking to partner with reliable CNC precision machining providers, companies like Deep Mould offer comprehensive solutions tailored to meet specific needs, ensuring high-quality outcomes and customer satisfaction.